Respect for Human Rights and Diversity
Basic Approach to Respect for Human Rights
The IWATSU Group believes that we must manage our businesses in a way that respects the human rights of all people involved in our business activities.
We believe that it is the IWATSU Group’s social responsibility to earnestly face and contribute to solving various risks related to human rights in the value chain, including the Group itself, and we are thus working to solve issues in this area.
Statement of Policy in Response to the ILO Core Labor Standards
Prohibition of Child Labor
Prohibition of any labor that interferes with compulsory education and dangerous and harmful labor by employees under the age of 18 subject to laws and regulations
Prohibition of Forced Labor
Prohibition of all forms of forced labor (forced, binding, inhumane bonded labor, etc.)
Elimination of Discrimination in Employment and Occupation
Prohibition of all forms of discrimination and harassment, and respect for the human rights of all employees
Freedom of Association and Respect for the Right to Collective Bargaining
Freedom of association and respect for the right to collective bargaining, and the promotion of smooth communication between labor and management
Overview of Activities Related to Respect for Human Rights
■ Formulation of Statement of Policy in Response to the ILO Core Labor Standards
IWATSU ELECTRIC and Iwatsu Manufacturing have formulated internal policies based on the “International Labor Organization (ILO) Declaration on the Fundamental Principles and Rights at Work,” and they endeavor to spread awareness and understanding of these policies, and ensure compliance with them.
■ Response to Modern Slavery Act
Even in modern times, there are many problems related to slavery, such as forced labor, where pressure from threats, violence, or other means is used to force people to work. In order to address the risk of “modern slavery” in our procurement process, the IWATSU Group is developing a set of procurement guidelines.
■ Education or awareness-raising activities related to human rights
IWATSU ELECTRIC believes that it is necessary to deepen understanding of human rights and a diverse range of values, and is taking steps to enhance related education and efforts to raise awareness.
Specifically, IWATSU ELECTRIC engages in initiatives such as education and awareness-raising to prevent harassment for employees of all levels of seniority, and education related to the importance of human rights in business for new employees.
■ Cooperation between labor and management
Labor unions have been formed at IWATSU ELECTRIC and Iwatsu Manufacturing.
Our basic stance is to respect the ILO Core Labor Standards and address various issues through dialogue between labor and management. Specifically, we exchange views and form agreements through discussions between labor and management, etc., on various issues related to management issues, personnel systems, workstyles, etc.
For companies in the IWATSU Group that do not have labor unions, we have selected labor representatives, who participate in dialogue between labor and management and have entered into agreements.
Proportion of unionized workers*
As of March 31 for each fiscal year
2018 fiscal year |
2019 fiscal year |
2020 fiscal year |
2021 fiscal year |
|
---|---|---|---|---|
IWATSU ELECTRIC CO., LTD. | 54.3% | 54.3% | 52.9% | 54.1% |
Iwatsu Manufacturing Co., Ltd. |
77.8% | 79.4% | 78.9% | 79.1% |
- The two companies in the table have adopted union shop systems.
Indicates the proportion of union members among full-time employees, including those in management positions.
Basic Approach to Respect for Diversity
Based on our view that striving for and developing a diverse range of human resources will contribute to enhancing corporate value over the medium and long term, the IWATSU Group hires and promotes the active participation of excellent human resources with future potential, regardless of nationality, gender, and disability.
Proportion of men and women by age group
As of March 31 for each fiscal year
Age group | Gender | FY2018 | FY2019 | FY2020 | FY2021 | |
---|---|---|---|---|---|---|
IWATSU ELECTRIC CO., LTD. | Younger than 30 years old | Male | 8.6% | 7.9% | 7.3% | 8.3% |
Female | 1.8% | 1.8% | 2.4% | 3.7% | ||
30~ 50 years old |
Male | 36.4% | 35.6% | 33.6% | 31.3% | |
Female | 5.3% | 4.3% | 4.0% | 3.9% | ||
50 years old or older | Male | 43.9% | 45.6% | 47.6% | 47.9% | |
Female | 4.0% | 4.8% | 5.1% | 4.9% | ||
IWATSU Group | Younger than 30 years old | Male | 9.0% | 8.8% | 8.5% | 9.5% |
Female | 6.4% | 7.2% | 7.1% | 8.3% | ||
30~ 50 years old |
Male | 32.1% | 30.8% | 29.4% | 27.5% | |
Female | 14.1% | 13.3% | 14.4% | 13.0% | ||
50 years old or older | Male | 26.6% | 27.8% | 28.5% | 29.5% | |
Female | 11.8% | 12.1% | 12.1% | 12.2% |
Overview of Activities Related to Respect for Diversity
■ Promotion of the active participation of women
IWATSU ELECTRIC hires employees for technical, administrative, and sales roles regardless of their gender. In recent years, the proportion of new employees who are women has been trending upward, thanks in part to stronger efforts to advertise to female students when hiring new graduates.
When appointing managers, we also make a comprehensive judgment of the candidate’s skills and experience, regardless of gender.
In order to retain female employees and increase the proportion of female managers, we will continue enhancing our internal environment and strengthening the development of human resources, as we further promote the active participation of women.
Proportion of women in new employees (IWATSU ELECTRIC)
As of March 31 for each fiscal year
FY2018 | FY2019 | FY2020 | FY2021 |
---|---|---|---|
22.2% | 30.0% | 36.4% | 27.8% |
Proportion of female employees in management roles (IWATSU ELECTRIC)
As of March 31 for each fiscal year
FY2018 | FY2019 | FY2020 | FY2021 |
---|---|---|---|
10.6% | 10.4% | 9.8% | 9.3% |
■ Hiring of foreign nationals
IWATSU ELECTRIC is strengthening hiring activities with the aim of securing human resources from a diverse range of cultural backgrounds, and is also endeavoring to enhance the internal environment and systems.
■ Hiring of disabled people
IWATSU ELECTRIC is focusing on hiring activities for disabled people, as well as efforts to support the retention of disabled employees after they join the Company. In this way, we are taking steps to stabilize and promote employment for disabled people.
Hiring rate of people with disabilities (IWATSU ELECTRIC)
As of March 31 for each fiscal year
FY2018 | FY2019 | FY2020 | FY2021 | |
---|---|---|---|---|
Statutory employment rate | 2.2% | 2.3% | ||
IWATSU ELECTRIC CO., LTD. | 1.2% | 1.3% | 1.7% | 2.4% |
■ Promoting active participation by senior employees
At IWATSU ELECTRIC, we have introduced a rehiring system for employees who retire upon reaching retirement age, enabling us to provide a workplace where ambitious and skilled human resources can continue to actively participate. Senior employees are essential human resources from the perspective of handing down technical expertise, so we will continue working to create opportunities and an environment that enables them to actively participate over the long term.
Human Resources Development
Basic Approach
The IWATSU Group believes that “people” are an asset, and that the growth of each and every employee will contribute to the growth of the Group. Accordingly, we have listed “human resources development and technological transfer” as one of the themes of our activities based on our areas of key sustainability issues. Based on this belief, we have developed education systems in each Group company and are endeavoring to enhance the skills and knowledge of our employees.
Overview of Activities
■ Development of human resources through the ICAP education program
IWATSU ELECTRIC has established the ICAP (Iwatsu training program for Creativity, Ability & Possibility) education program, and is using it to provide opportunities for growth. We are utilizing ICAP to promote the development and training of human resources who will contribute to the achievement of our business targets.
Specifically, in addition to on-the-job training (OJT), we also provide education for employees at each level of seniority, in order to develop employees’ awareness of expected roles at each stage of growth. We have also created systems to support the development of individual skills. These support systems mainly support the enhancement of business skills and employees’ career formation.
ICAP system diagram
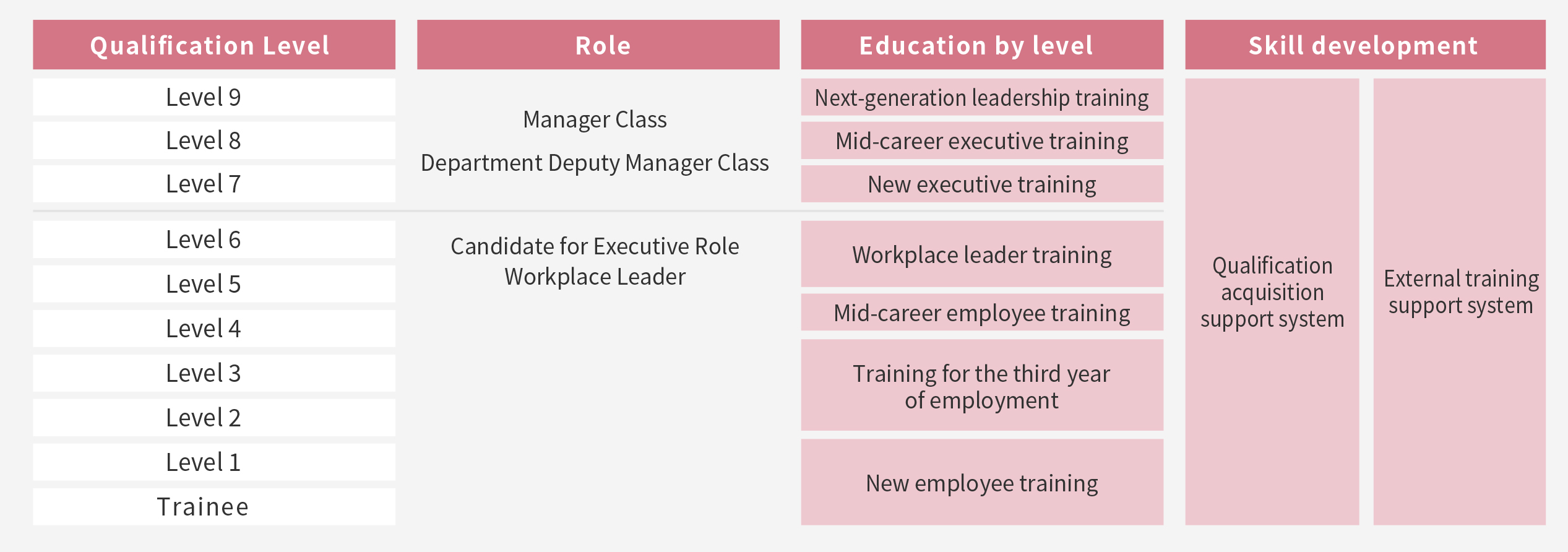
Previously, our system for supporting participation education by external institutions was based on group seminars and e-learning, but as a result of the COVID-19 pandemic, we have shifted from group seminars to online seminars. We will continue developing human resources through education suited to the new normal.
Number of courses taken (number of times the system for supporting participation in education by external institutions was used)
FY2018 | FY2019 | FY2020 | FY2021 | |
---|---|---|---|---|
Number of courses taken | 79 | 106 | 59* | 94 |
- The number of courses taken fell because group events were cancelled as a result of the COVID-19 pandemic.
Educational programs in which employees may participate
- Corporate planning
- Personnel and labor
- Accounting, finance, and taxation
- General affairs, legal affairs, audits
- Sales and marketing
- Trade and logistics
- Business skills (logical thinking, negotiating, business manners, communication, PC skills, etc.), etc.
■ Specialist education
IWATSU ELECTRIC plans and implements specialist education and training related to operations in administrative, development, sales and marketing, and production management departments.
Examples of education in fiscal 2021
- Design-related education (circuit design, structural design, software design, wireless technologies, etc.)
- New product education (sales, maintenance services, etc.)
- Quality management, product safety-related education
- Chemical substance management and SDS education
- Trade management education
- Information systems-related education
- Intellectual property-related education
- JIS Q 9100-related education
■ Development of human resources involved in manufacturing processes
Iwatsu Manufacturing plans and conducts education to support the acquisition of necessary knowledge and skills for manufacturing processes and the development of human resources who will contribute to improving operations and enhancing productivity. At a training center established within the company, Iwatsu Manufacturing provides education and training on specific themes, as part of efforts to enhance the skills and knowledge of employees.
By deploying the skills and knowledge developed at Iwatsu Manufacturing to Iwatsu Malaysia, our overseas plant, the company is also contributing to enhancing production technical expertise in the Group as a whole.
Examples of education at the training center in fiscal 2021
- TWI training (how to teach and improve work)
- Solder knowledge
- Soldering skill acquisition
- Quality management education
- General work rules education
- Shipping operations basic rules and precautions etc.
Health and Productivity Management and Work-Life Balance
Basic Approach
The IWATSU Group believes that ensuring that each and every employee is able to actively participate with a sense of vitality will contribute to enhancing corporate value. To ensure that all employees can sufficiently exercise their respective skills and capabilities, we are developing systems and measures to support the balance of physical and mental health and a fulfilling life and work.
Overview of Activities
■ Health support
In addition to statutory health checks, IWATSU ELECTRIC has also been conducting stress checks since fiscal 2016. The Company is creating a system to care for the physical and mental health of employees, including establishing a Health Support Office within the Company and creating days for health consultations with public health nurses and occupational health physicians, as well as promoting health promotion programs together with health insurance associations.
Examples of programs to promote health
- Online no smoking program
- Walking event
■ Support for giving birth, raising children, and nursing care
For employees who are giving birth, raising children, or caring for relatives, IWATSU ELECTRIC has created leave systems, shortened working hour systems, and offset shift systems that employees can use regardless of whether they are male or female, in addition to statutory leave systems. In this way, we are supporting the balance between home and work.
Systems to support employees giving birth, raising children, or caring for relatives
- Morning sickness leave system
- Shortened working hours during pregnancy system
- Maternity leave (pre- and post-pregnancy)
- Childcare leave and temporary suspension of work system
- Offset shift system for childcare
- Shortened working hour system for childcare and nursing care
- Nursing leave for children until they graduate from elementary school (can also be acquired in half-day and hourly units)
- Multi-purpose leave system for participation in school events and cases when children’s schools are closed, until they graduate from elementary school
- Relative nursing care leave
- Nursing care temporary suspension of work system (can also be acquired in half-day and hourly units)
Number of employees who took time off work for childcare (IWATSU ELECTRIC)
Number of persons who took leave / eligible persons
FY2018 | FY2019 | FY2020 | FY2021 | |
---|---|---|---|---|
Male | 2 / 6 people | 1 / 8 people | 0 / 3 people | 2 / 4 people |
Female | 0 / 0 people | 0 / 0 people | 1 / 1 people | 1 / 1 people |
Rate of employees returning to work after time off for childcare (IWATSU ELECTRIC)
As of March 31 for each fiscal year
FY2018 | FY2019 | FY2020 | FY2021 |
---|---|---|---|
100% | 100% | - | 100% |
■ Promotion of flexible workstyles
In order to make more flexible workstyles a reality, in fiscal 2021, IWATSU ELECTRIC introduced a system that allows employees to take paid leave in units of one hour. The company is also actively working to prevent long working hours, including enhancing various types of leave system and setting days with company-wide finishing times.
Main systems and measures
- Refresher leave system
- Multi-purpose leave (available for public volunteer activities and volunteer activities related to raising the next generation, such as schools and local communications)
- Paid leave uptake campaign (June)
- Days with company-wide finishing times (second and fourth Friday of every month)
Average number of days of paid leave taken (IWATSU ELECTRIC)
FY2018 | FY2019 | FY2020 | FY2021 |
---|---|---|---|
11.0 days | 11.0 days | 12.0 days | 12.4 days |
■ Promotion of new workstyles in anticipation of the post-COVID-19 age
IWATSU ELECTRIC introduced teleworking as part of countermeasures against COVID-19. We are taking steps to establish new workstyles, by distributing laptop computers to all employees and enhancing our environment for remote access. In September 2021, the Company opened a satellite office (Minato-ku, Tokyo), partly to support employees working remotely.
Satellite office (Prime Terrace KAMIYACHO)
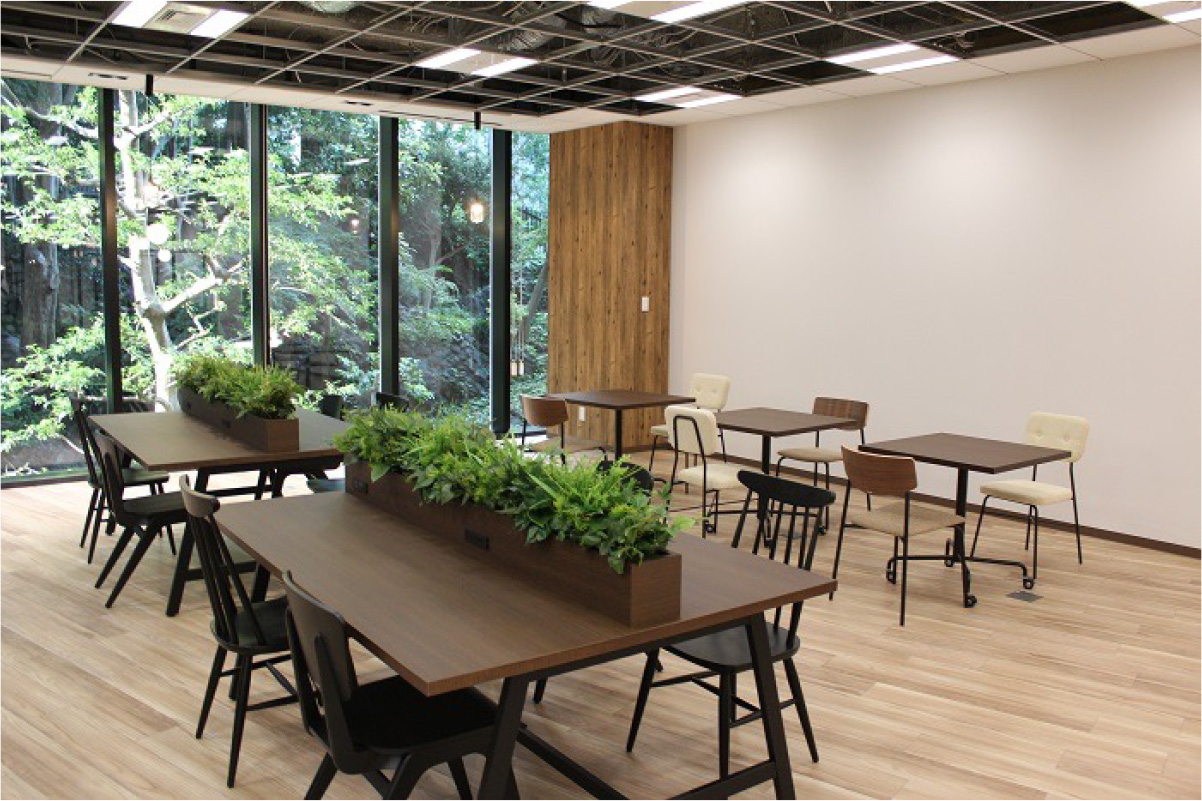
Occupational Health and Safety
Basic Approach
To ensure that each and every employee can enjoy peace of mind as they work and exercise their abilities, the IWATSU GROUP believes it is important to develop, maintain, and enhance occupational health and safety in the workplace. We are promoting the creation of a comfortable workplace environment that meets employees’ needs from a social, psychological, and physical perspective, by working to prevent illness and occupational injury among employees in advance, and tackling causes of stress, etc.
Promotion system
IWATSU ELECTRIC and Iwatsu Manufacturing have established systems to manage health and safety, in order to prevent occupational injury and promote the creation of a comfortable workplace environment.
IWASAKI ELECTRIC has established a Health and Safety Committee, whose members include the Manager Responsible for General Health and Safety, occupational health physicians, representatives of labor unions, and the Secretariat. Representatives of health insurance associations also participate as observers. The Company endeavors to share and enhance awareness of the content of this committee’s deliberations and reports among employees, through internal newsletters and the intranet, as necessary.
Iwatsu Manufacturing has established Health and Safety Committees at each business site. The members of these committees consist of safety mangers, sanitation managers, occupational health physicians, representatives of labor unions, and the Secretariat. Iwatsu Manufacturing has also established Workplace Health and Safety Committees at two business sites, and the members of these committees play an active role.
Health and safety management organization chart (IWATSU ELECTRIC)
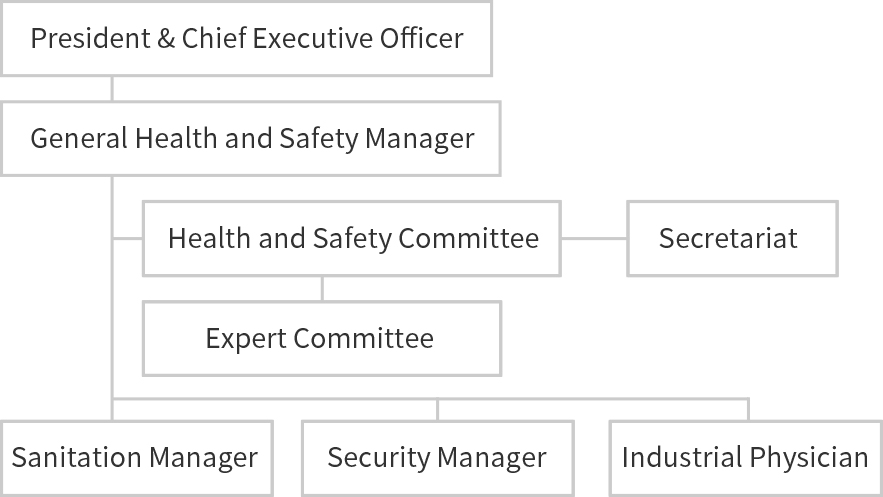
Health and safety management organization chart (Iwatsu Manufacturing)
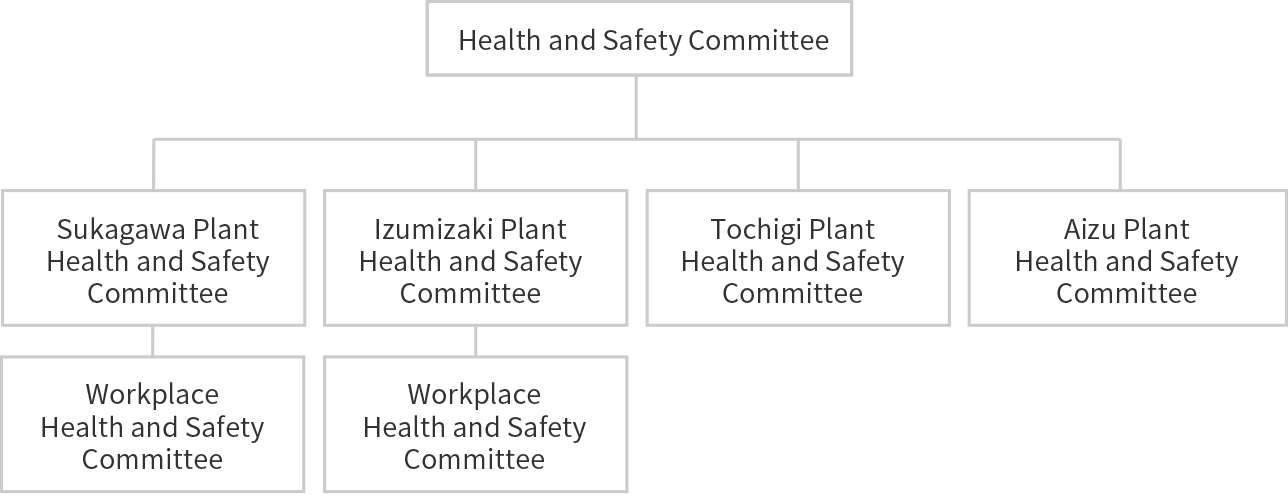
Overview of Activities
■ Stress checks
As part of measures to address mental health, IWATSU ELECTRIC holds stress checks for employees once a year. Due consideration is also given to privacy, to ensure that the Company does not obtain the results of stress checks without the subject’s consent.
■ Risk assessment for chemical substances
Once a year, IWATSU ELECTRIC performs chemical substance risk assessments for departments that use solder, chemical solvents, and other chemical substances.
Chemical substances are mainly used in design and development. Assessments conducted in July 2021 showed that no highly harmful substances are in use, and the amounts used of chemical substances are also low. As a result, no workplaces were found to present a high risk to health.
We also perform similar assessments at Group companies that use chemical substances for manufacturing, repair, etc. Based on the results of assessments at each company, we introduce protective equipment and improve facilities, while also endeavoring to reduce the usage of harmful chemical substances used in manufacturing processes and the risk of exposure.
■ Initiatives to prevent fire and disaster
Once a year, each IWATSU Group company holds fire and disaster prevention drills.
In addition to statutory drills, IWATSU ELECTRIC also works to spread awareness throughout the Company of how to use AEDs and disaster prevention equipment, what to do in the event of disaster, etc., as part of its endeavor to increase awareness of disaster prevention.
Fire and disaster prevention drills
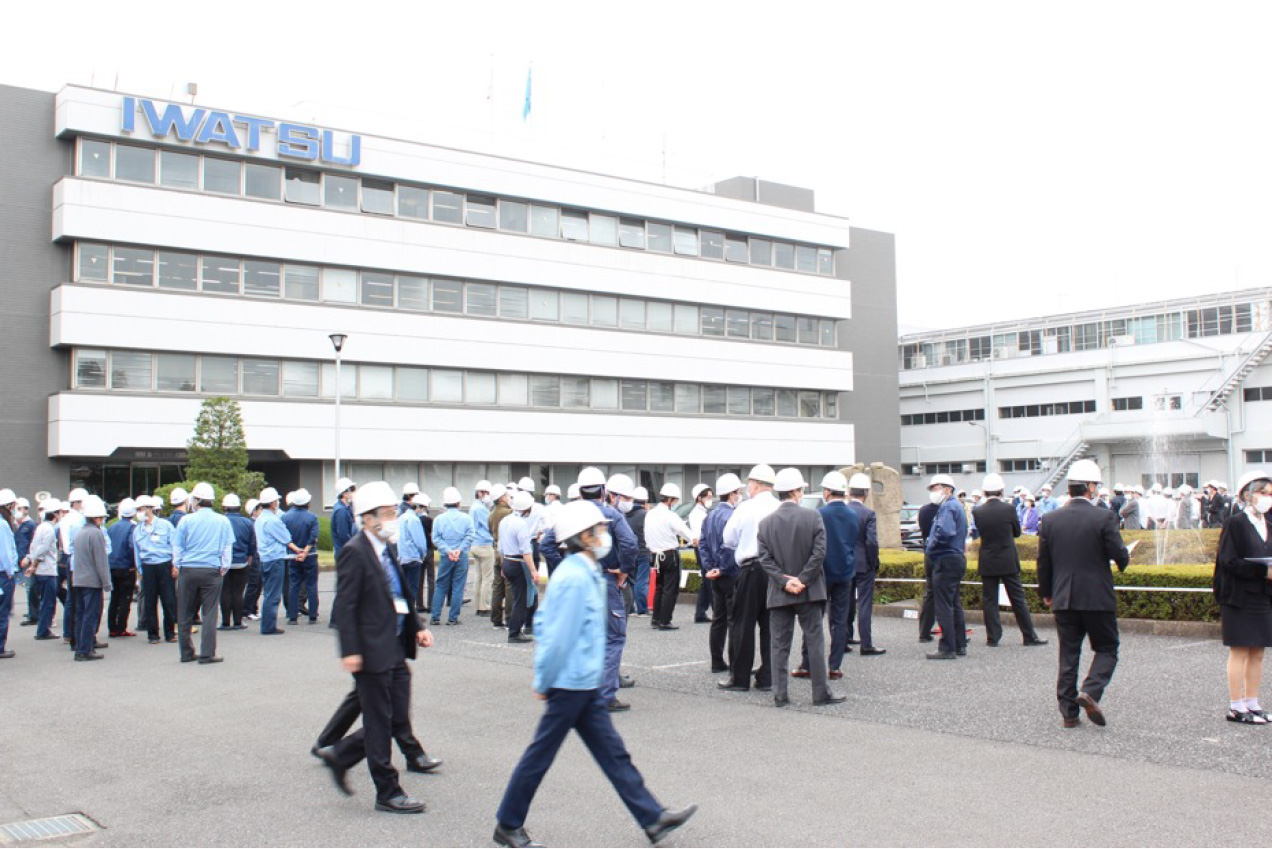
AED hands-on learning
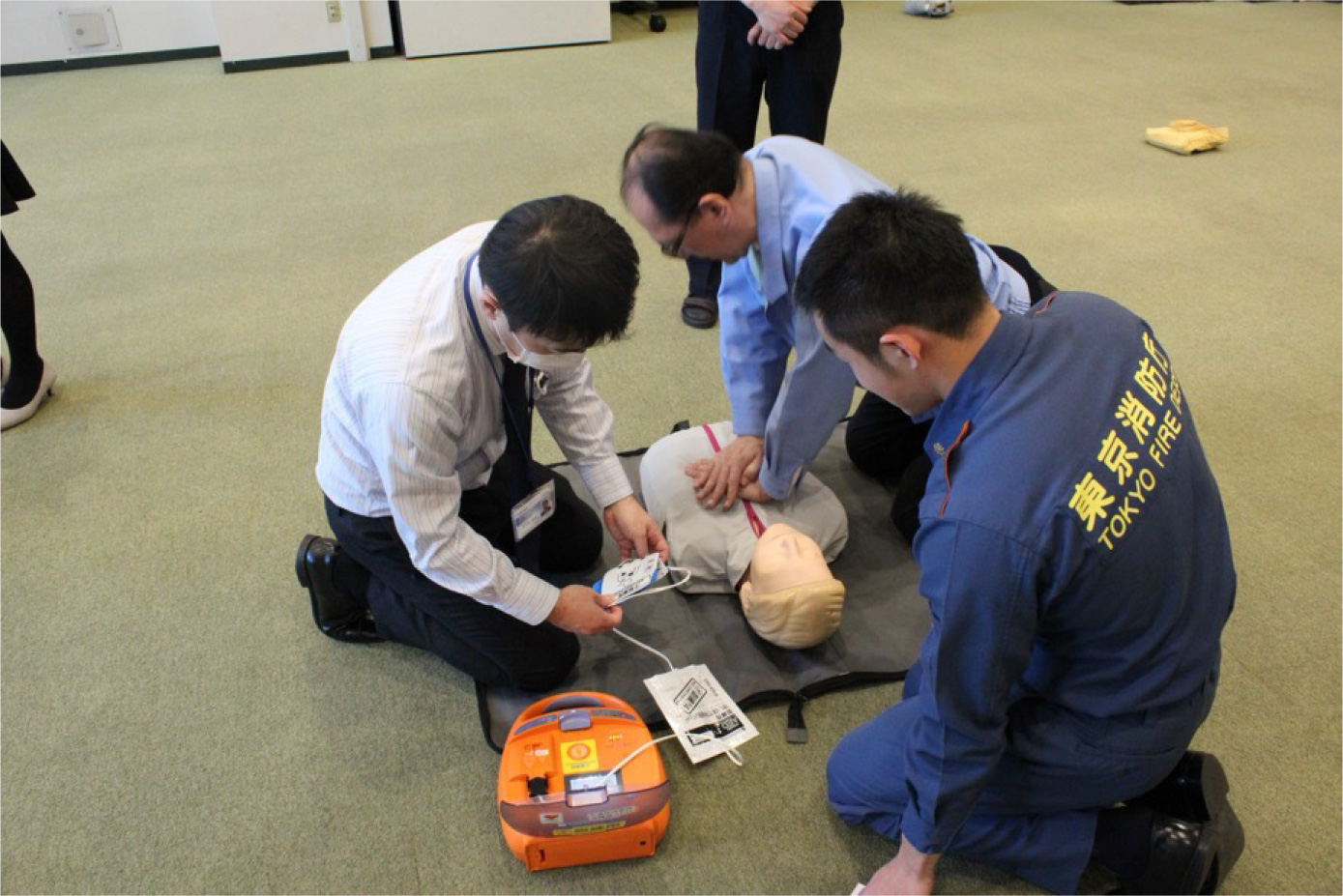
(both at IWATSU ELECTRIC)
■ Prevention of occupational and commuting injuries
Iwatsu Manufacturing, which has production plants, places the utmost priority on the safety of employees, and ensures that there are inspections before work starts and safety patrols. This company also endeavors to increase awareness of safety and prevent occupational injury by providing education on the safe use of production equipment and chemical substances.
IWATSU ELECTRIC holds safe driving courses once a year, in order to protect the safety of employees who drive for commuting and work, and promote traffic safety. In fiscal 2021, the company held courses on “driving while using a smartphone” and “driving at dusk.” Going forward, we will continue working to ensure that employees are mindful of complying with traffic rules and practicing good transport etiquette.
Number of occupational and commuting injuries*
FY2018 | FY2019 | FY2020 | FY2021 | ||
---|---|---|---|---|---|
IWATSU ELECTRIC CO., LTD. | Occupational injury | 1 | 1 | 1 | 0 |
Commuting injuries | 0 | 1 | 1 | 1 | Iwatsu Manufacturing Co., Ltd. |
Occupational injury | 2 | 4 | 1 | 4 |
Commuting injuries | 0 | 0 | 0 | 0 |
- Includes minor incidents that resulted in less than one day of work lost. Between fiscal 2018 and 2021, only one occupational injury requiring compensation for time off work occurred at Iwatsu Manufacturing, in fiscal 2021.
■ Initiatives against COVID-19
The IWATSU Group’s countermeasures against COVID-19 include the promotion of teleworking, a shift from group meetings to online meetings, the placement of acrylic sheets to prevent droplets, and thorough measures to circulate air.
Iwatsu Manufacturing has also been taking steps to prevent infection, while prioritizing business continuity, by using antibody test kits on visitors at the time of entry.
IWATSU ELECTRIC has also placed our own brand of alcohol disinfectant, “ALMEE,” within the company, and is using it for hand sanitization.
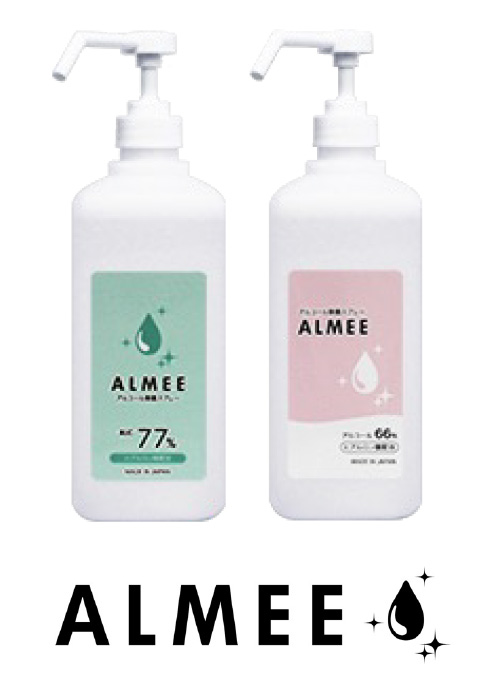
Supply Chain Management
Basic Approach
In the corporate environment of our time, globalization has accelerated, making it important to address global issues including issues related to human rights, the environment, pandemics and the increasing severity of natural disasters associated with climate change. At the IWATSU Group, we respond to social requirements by working together with all of the trading partners involved in our supply chain, including in the procurement of parts and materials, development, production, sales, services and recycling, aiming to build a sustainable society and increase our competitiveness.
Sustainable Material Procurement Policy
- We will conduct business in good faith with all trading partners in Japan and overseas by fairly providing them with opportunities and observing related laws, regulations and contracts from a position of equality with them.
- We will conduct procurement prioritizing trading partners who agree to and comply with the IWATSU Group Sustainable Procurement Guidelines.
- We will procure competitive products and services based on economic efficiency by comprehensively judging the quality, ability to observe delivery dates and ensuring stable supply, price, technological and service skills and corporate stances to improve capabilities in these areas.
- We will take thorough information security measures to protect trading partners' personal information and confidential information that we obtain in the course of business.
- We will deepen mutual understanding and build relationships of trust with all trading partners and act together with them to contribute to the establishment of a sustainable society.
Overview of Activities
■IWATSU Group supply chain management
Almost all products offered by the IWATSU Group are manufactured at one of five production sites (four in Japan and one overseas), with materials procured from numerous trading partners in Japan and overseas.
Under our Sustainable Material Procurement Policy, we inform our trading partners of our Sustainable Procurement Guidelines, request that they implement initiatives accordingly, and audit their plants to manage the quality of the procured goods, thus promoting supply chain management.
Main procured items at productin sites
- Electronic components
- PCBs
- Molded resin products
- Sheet metal materials and processed sheet metal products
- Chemicals
■Materials seminars
At the IWATSU Group, we hold yearly materials seminars to share our business policies and approach to new business development and procurement with trading partners and to promote business activities together with them.
■Sustainable Procurement Guidelines and Green Procurement Standards
At the IWATSU Group, we established the IWATSU Group Sustainable Procurement Guidelines and the IWATSU Group Green Procurement Standards which supplement the guidelines in January 2023 in light of the social situations related to sustainable procurement in recent years.
We promote sustainable procurement by prioritizing business partners who support and comply with these guidelines.
■Responsible minerals procurement
Because some of the minerals mined in the Democratic Republic of the Congo and surrounding countries are used as a source of funds for armed groups that commit inhumane acts, the US Financial Regulatory Reform Act (Dodd-Frank Act) and the EU Conflict Minerals Regulations have been enacted.
Also, there is a growing movement to require companies to conduct due diligence to ensure that the mineral resources they procure do not promote conflict or human rights violations.
For example, the OECD requires all companies to responsible minerals procurement based on the "OECD Due Diligence Guidance for Responsible supply Chains of Minerals from Conflict-Affected and High-Risk Areas".
In order to fulfill our social responsibility in procurement activities, the Iwatsu Group will continue to promote efforts to eliminate the use of conflict minerals as a source of funding for armed groups, with our business partners while ensuring transparency in our supply chain.
- 1)Serious abuses associated with the extraction, transport or trade of minerals
- 2)Direct or indirect support to non-state armed groups
- 3)Illegal acts by public or private security forces
- 4)Bribery and fraudulent misrepresentation of the origin of minerals
- 5)Money laundering
- 6)Non-payment of taxes, fees and royalties due to governments
- ① Republic of South Sudan, ② Republic of Uganda, ③ Republic of Rwanda, ④ Republic of Burundi, ⑤ United Republic of Tanzania, ⑥ Republic of Zambia, ⑦ Republic of Angola, ⑧ Republic of the Congo, ⑨ Central African Republic
Iwatsu Group Responsible Minerals Procurement Policy
Our group has established and operates a management process in line with the OECD's due diligence guidance for the following minerals contained in parts and materials we procure and their associated risks, in order to avoid promoting conflicts and human rights violations. By doing so, we will contribute to international efforts towards responsible mineral sourcing.
For this reason, we regularly conduct surveys of our group's supply chain using the CMRT (Conflict Minerals Reporting Template) of the Responsible Minerals Initiative (RMI), which is a standard form for conflict minerals surveys.
If a risk is identified, we will continue to take steps within commercially reasonable limits, such as changing to parts and materials with less risk.
Target minerals
Tin, Tantalum, Tungsten, Gold, and minerals judged by our group to be at high risk due to social conditions, etc.
Risks covered
Quality Management
Basic Approach
The IWATSU Group believes that it is important that we work to resolve social issues and contribute to achieving a sustainable society by providing high-quality and highly safe products and services. Based on this approach, we have established a Quality Policy, and we are working to enhance the quality of our products and services as well as customer satisfaction.
Quality Policy
The IWATSU Group will contribute to social progress and development by offering high-quality products and services centered on “connecting,” “measuring,” and “communicating.”
We will strive for technological innovation, to enable us to develop attractive products and services, and fulfill the needs of society and our customers.
We will endeavor to increase customer satisfaction through improvements to the quality of our products and services.
We will endeavor to achieve efficient business management and improvements in management indicators by improving the quality of our operations.
We will endeavor to develop human resources, in order to achieve technological innovation and enhance the quality of our products, services, and operations.
We will improve our quality management system on an ongoing basis, in accordance with the requirements of standards, our customers, and other requirements.
- The above Quality Policy applies to ISO 9001-certified organizations in Japan.
QMS Promotion System
In the IWATSU Group, we have created a quality management system (QMS) based on ISO 9001, and we are now operating and managing this system as part of our efforts to ensure quality and enhance customer satisfaction.
Under the direction of the manager responsible for the QMS, the Group Secretariat coordinates with each department and internal auditors to promote continuous performance improvements through internal audits, management reviews, and other measures.

Status of acquisition of ISO 9001
Company name | Status of acquisition | Certification body / number |
---|---|---|
IWATSU ELECTRIC CO., LTD. | ○ |
JIC Quality Assurance Ltd. / 3773 |
Iwatsu Manufacturing Co., Ltd. | ○ |
|
IWATSU NETWORK SOLUTION CO., LTD.* | ○ |
|
IWATSU Business Services Co., Ltd. | ○ |
|
IWATSU SYSTEM & SOFTWARE CO., LTD. | ○ |
|
Tohtsu Industry Co., Ltd. | × |
|
Dentsu Service Co., Ltd. | × |
- |
groxi Inc. | × |
- |
Iwatsu (Malaysia) SdnBhd | ● |
SIRIM/QMS 02860 |
* Including sales sites
○: Acquired as Group certification by the head office of IWATSU ELECTRIC●: Acquired as individual certification. Iwatsu (Malaysia) Sdn Bhd has developed and operates a separate QMS promotion system to that of our operations in Japan
■ Internal audits
Once a year, the head office of IWATSU ELECTRIC leads a review of the conformity and effectiveness of the IWATSU Group’s QMS.
[Implementation time] August to October 2021*
[Subject] 14 sites across six companies (IWATSU Group, in Japan)
[Results] No major non-conforming items
- Implemented as an integrated audit together with the EMS
■ External inspections
Once a year, the IWATSU Group receives an external inspection of the conformity and effectiveness of our QMS from a certification body. We correct or rectify any non-conforming items within a predetermined period. Each department addresses opportunities for improvement, and the status of their response is confirmed in internal audits.
[Implementation time] February 2022
[Certification body] JIC Quality Assurance Ltd.
[Results] Non-conforming items: 0; opportunities for improvement: 27
■ Management review
Twice a year, the IWATSU Group Secretariat leads management reviews within the Group. Senior management receives reports on matters such as the status of achievement of quality targets, the monitoring of customer satisfaction, and points for improvement related to the QMS.
[Implementation time] April 2021 (summary for the previous fiscal year*)
January 2022 (internal audit report*)
- Implemented as an integrated report together with the EMS
■ Initiatives targeting quality improvements
The Quality Satisfaction Dept. of the head office of IWATSU ELECTRIC leads efforts to reduce product defects and enhance process quality, in coordination with plant quality departments and manufacturing departments.
Senior management receives direct reports on the status of market quality and process quality at regular meetings of the Quality Committee, as part of efforts to appropriately share information and respond promptly.
■ Prevention of product accidents
The IWATSU Group has put in place internal regulations that we have developed to enable us to respond promptly and appropriately to any major accidents or emergencies related to our products. In addition to spreading awareness of whistleblowing rules through pages on the internal intranet, we also use education to promote the thorough implementation of these rules.
We also endeavor to provide timely and appropriate disclosure and information concerning product recalls on our website.
In fiscal 2021, there were no quality accidents that had any significant impact on the assets of our customers.
■ Prevention of violation of laws and regulations
We assess the status of compliance with laws and regulations related to our products through design inspections and verification by engineering departments, as well as checks of validity by quality satisfaction departments.
■ Quality education
In order to effectively operate our QMS, the IWATSU Group plans and executes education and awareness-raising activities for quality month.
Status of implementation in fiscal 2021
Name of education or awareness-raising activity | Number of participants (people) |
---|---|
Education for new employees (overview of EMS) | 20 |
Quality month education (oral explanations of the Check and Act process) | 38 |
“Organizational Knowledge” | 48 |
Advance education for internal audits | 72 |
New internal auditor development education | 14 |
Interpretation of the ISO 9001:2015 standard (e-learning)* | 21 |
- Service provided by the QMS Committee of the Communications and Information Network Association of Japan
■ Customer satisfaction surveys by sales departments
Each sales department in IWATSU ELECTRIC gathers information on the views and desires of customers and sales agents regarding IWATSU products and services, and reflects them in its business activities. The company uses analysis of these views, etc., to improve the performance of products, quality, and level of service.
Community Contribution Activities
Each and every member of the IWATSU Group promotes coexistence and communication with local communities by actively engaging in regional and social contribution activities as a good corporate citizen.
■ Examples of IWATSU ELECTRIC activities
Participation in regional bodies
Takaido Police Relations Society, Takaido Police Safe Driving Managers Association, Ogikubo Hazardous Materials and Disaster Prevention Association, Ogikubo Fire Prevention Society, etc.
Installation of temperature monitoring system for COVID-19 vaccine freezers in community vaccination centers under the jurisdiction of Suginami City Office
Provision of emergency materials support sites for disasters (Suginami-ku disaster support plan)
Sponsor of Suginami Charity Walk
Support for Kugayama Firefly Festival
Support for spring / fall nationwide traffic safety campaigns, etc.
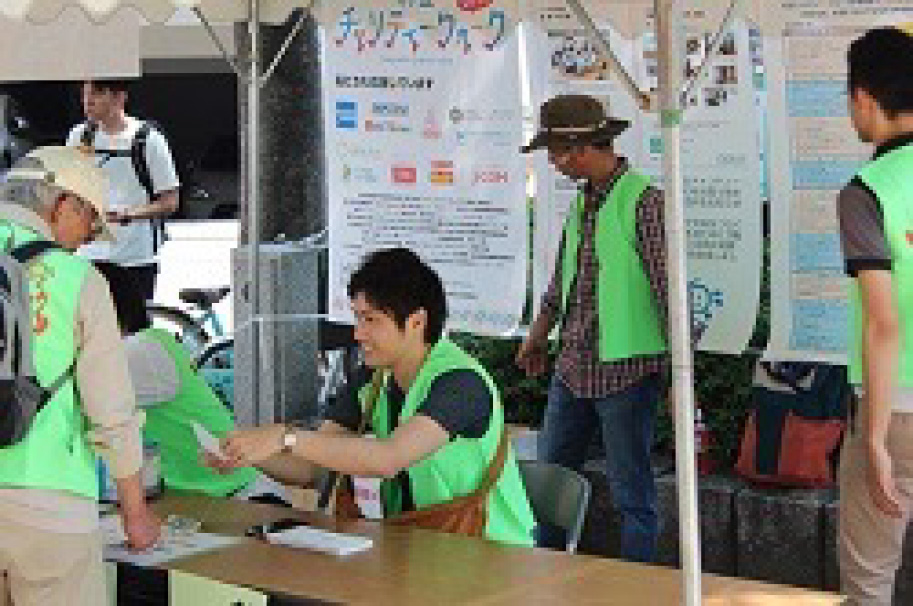
The Suginami Charity Walk and Kugayama Firefly Festival were suspended in fiscal 2020 and fiscal 2021 as a result of the COVID-19 pandemic. The photograph is from fiscal 2019.
■ Installation of temperature monitoring system for COVID-19 vaccine freezers in community vaccination centers under the jurisdiction of Suginami City Office
IWATSU ELECTRIC provided Suginami City with systems for monitoring the temperature of freezers for storing COVID-19 vaccines.
There were issues related to the management of “vaccine freezers,” including reports of vaccines being disposed of because of electrical problems.
These systems combine a USB camera with IWATSU’s “Keiki Yomu Zo” automatic meter reading software to read and constantly log temperatures in freezers, and automatically send out alert emails if it detects any abnormal temperatures.
This prevents the waste of vaccines by making it possible to quickly identify and respond to any issues, even in the early morning, at night, and other times when workers are not present.
- As of October 2022, this system is in operation at all community vaccination centers managed by Suginami City, excluding medical institutions.
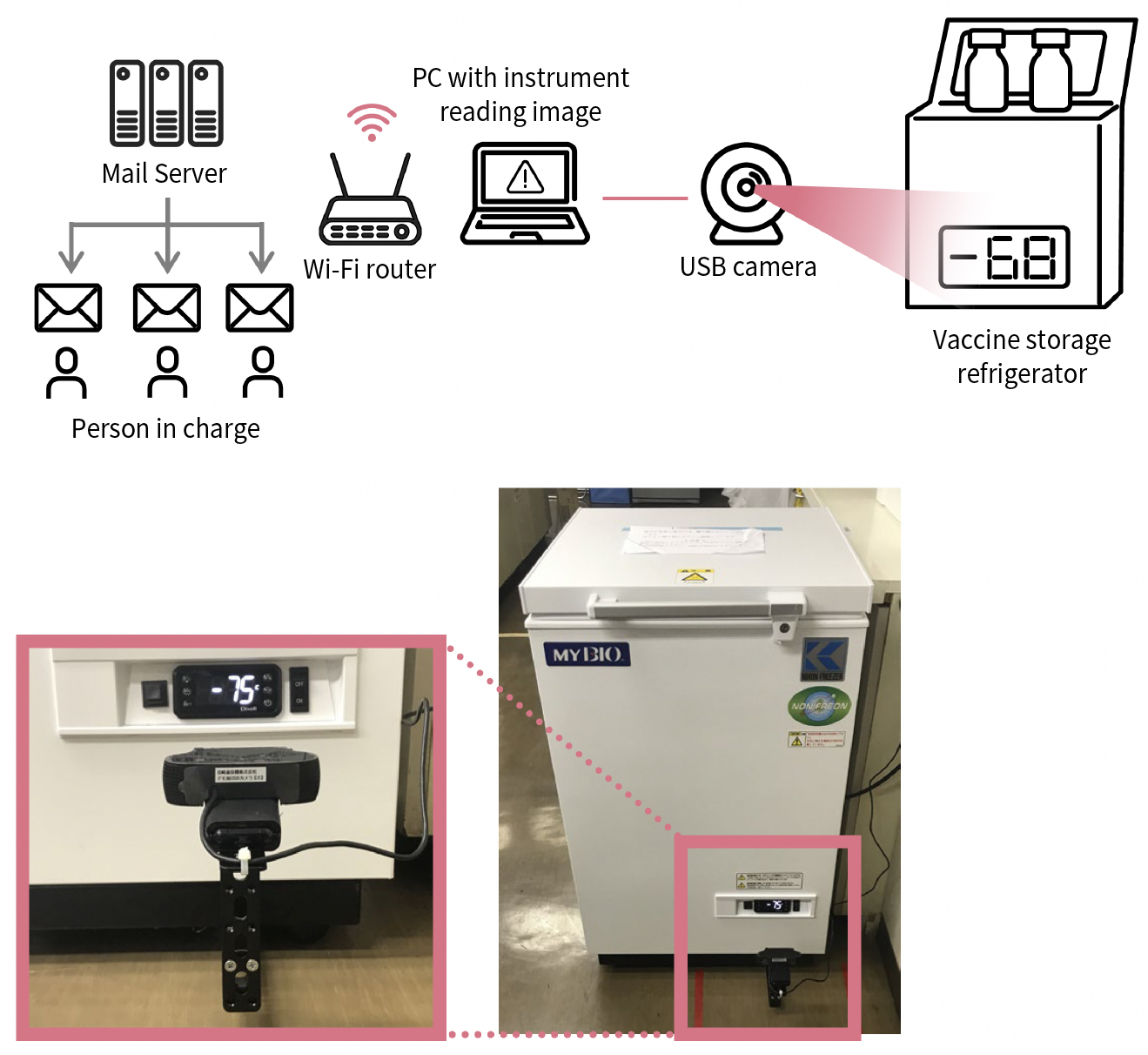
■ Iwatsu Manufacturing activities
Participation in regional bodies
Sukagawa Zone & Shirakawa Zone Police Supporters Association, Sukagawa Regional Fire Fighting and Disaster Prevention Society, Sukagawa Business Association for Safe Driving Management, Shirakawa Zone Fire Fighting Management and Liaison Council, etc.Participation in Matsuaki Akashi (one of the three great fire festivals of Japan)
Participation in the Tsuburaya Memorial Marathon
Flower-planting and beautification activities around plants
Eco cap activities
Support for blood donations in the workplace
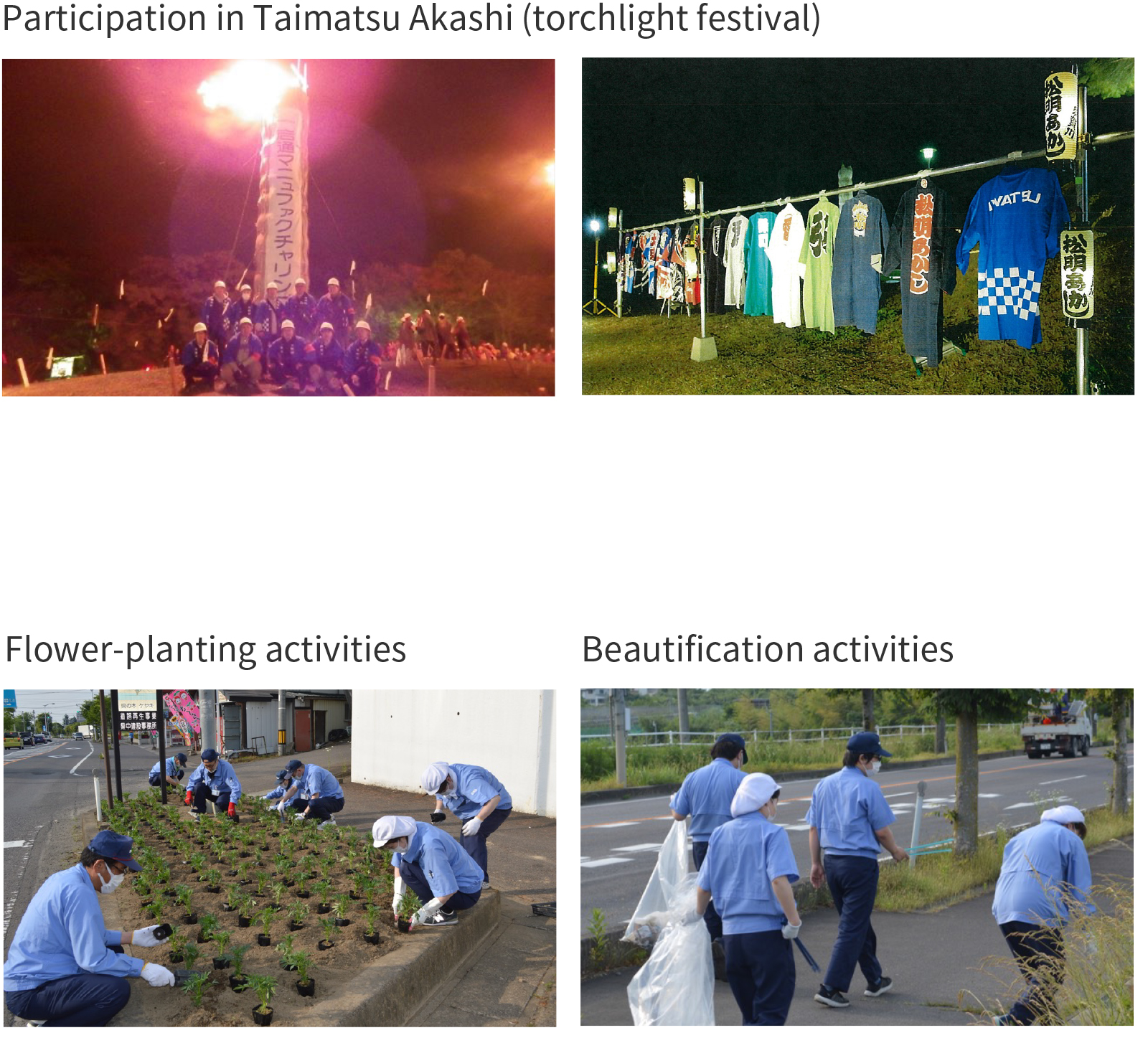